Can Migraine Cause Dizziness?
To answer the question “Can migraines cause dizziness?” is to delve into the intricate landscape of a neurological disorder that…
Science:
Subscribe to Our newsletter
Enter your email and we’ll keep you posted with news and updates!
Related Post
rajkotupdates.news : corona third wave affect life insurance
The ongoing pandemic has caused widespread anxiety about the future, including financial security. With the third wave of COVID-19 looming…
Latest
AR and VR Jackpots: Immersive Experiences in Online Slot Adventures
As technology continues to evolve, the world of online gaming is experiencing a revolutionary transformation through Augmented Reality (AR) and…
Hola Custom Boxes Packaging – Ensuring Quality and Utility in Each Box
Are you looking for packaging that delivers both quality and functionality? Look no further than Hola Custom Boxes Packaging. With…
How to Purchase Bitcoin
Getting started trading Bitcoin can seem intimidating, but it’s pretty easy. Trading crypto like Bitcoin and Tether BTC USDT only…
rajkot update news : link-aadhaar-with-voter-list
The Rajkot administration has recently issued a new directive to the citizens of Rajkot. The directive asks the voters to…
rajkot updates news during the sixth phase of vibrant gujarat summit 135 mous were signed
Rajkot, a city in the western Indian state of Gujarat, shone bright during the sixth phase of the Vibrant Gujarat…
rajkotupdates.news : corona third wave affect life insurance
The ongoing pandemic has caused widespread anxiety about the future, including financial security. With the third wave of COVID-19 looming…
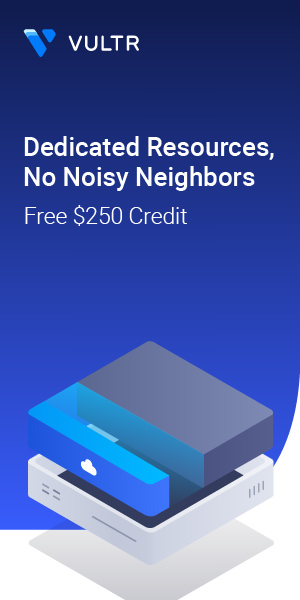